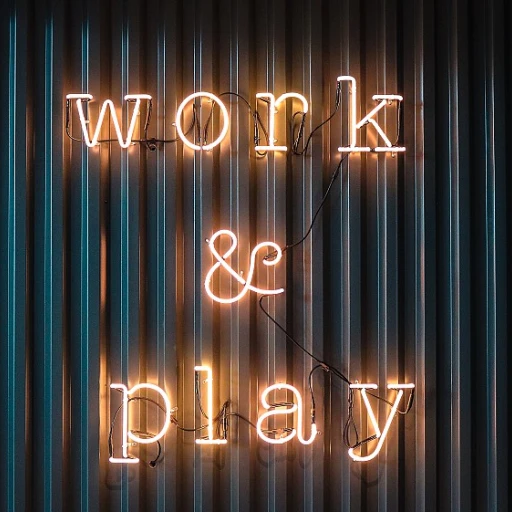
The Core Principles of Operational Excellence
Understanding the Core Elements of Operational Excellence
Operational excellence isn't just a buzzword; it's a critical philosophy that drives long-term business success. At its essence, it's about creating a culture of continuous improvement and efficiency. But what does that look like in practice?
Implementing Continuous Improvement for Sustainable Success
The principle of continuous improvement is the heartbeat of operational excellence. According to research, companies embracing this principle can see productivity increases of up to 30%. The Shingo Model, developed by Dr. Shigeo Shingo, is a proven framework that helps organizations achieve continuous improvement by focusing on five key principles—cultural enablers, continuous process improvement, enterprise alignment, results, and customer focus.
Key Metrics and Standards to Monitor
To gauge the effectiveness of operational excellence initiatives, robust metrics are essential. W. Edwards Deming's 14 Points for Management stresses the importance of setting clear standards and using data-driven insights to make informed decisions. For example, companies consistently monitoring key performance indicators (KPIs) related to process efficiency, employee engagement, and customer satisfaction often outperform their competitors.
Operational Excellence Requires Employee Engagement
One of the core principles of operational excellence is empowering employees. According to a study by the Institute for Operational Excellence, businesses with highly engaged employees reported 21% higher profitability and a 41% reduction in absenteeism. Engaged employees are more likely to innovate, solve problems efficiently, and provide a better customer experience.
Customer-Centric Processes for Enhanced Satisfaction
Focus on the customer is another cornerstone of operational excellence. Companies leveraging customer feedback to refine their processes often see an immense boost in customer satisfaction and loyalty. For instance, Amazon's obsession with customer satisfaction has played a huge role in its operational success. They continuously adapt their processes based on customer insights, leading to streamlined workflow, reduced delivery times, and higher quality service.
True Stories: Companies Mastering Operational Excellence
Some companies have become paragons of operational excellence. Toyota and Motorola are often cited in this regard due to their early adoption of lean principles and Six Sigma methodologies. The results? Remarkable improvements in process efficiency, product quality, and customer satisfaction.
Trends Indicating the Future of Operational Excellence
As businesses continue to evolve, the future of operational excellence will likely involve more advanced technologies and data analytics. A McKinsey report suggests that integrating AI and machine learning into operational processes will potentially yield an additional $3.5 trillion to $5.8 trillion in value annually. These innovations can help companies maintain a competitive edge by optimizing workflows and pushing the boundaries of what operational excellence can achieve.
Lean Manufacturing: A Path to Operational Efficiency
Understanding Lean Manufacturing
Lean manufacturing stands as a pivotal method for driving operational efficiency. Originating from Toyota's Production System, it is viewed as a guiding light in reducing waste while enhancing productivity. The effectiveness of the lean method is not just folklore; it is grounded in empirical evidence. According to a study by McKinsey, companies that implement lean processes witness a 50% reduction in operating costs and a 30% increase in quality.
The Core Principles of Lean Manufacturing
Everything about lean manufacturing revolves around the elimination of waste and the optimization of processes. Dr. Shigeo Shingo, a Japanese industrial engineer considered one of the founding fathers of lean manufacturing, emphasized 'continuous improvement' (Kaizen) as its core. The Shingo Model, thus, forms the bedrock of lean principles, making it a paragon for enterprises targeting operational excellence.
1. Value – Understanding and defining what is valuable to the customer.
2. Value Stream – Mapping out all steps in the processes to determine the value-added steps versus waste.
3. Flow – Ensuring that workflows smoothly through all production operations.
4. Pull – Letting customer demand drive production.
5. Perfection – Pursuing perfection through continuous improvement.
Real-World Examples and Results
Many global giants have achieved operational excellence by deploying lean manufacturing principles. Toyota, for instance, reported a 15% increase in customer satisfaction due to streamlined operations and superior product quality. Similarly, Motorola attributed its 20% cost savings to lean methodologies implemented across its production lines.
Expert Insights on Lean Manufacturing
W. Edwards Deming, recognized for his work with Toyota and other Japanese manufacturers post-WWII, famously said, 'Quality is everyone's responsibility.' This resonates deeply within the lean context as it emphasizes collective accountability for continuous improvement. Experts from Utah State University's Shingo Institute further stress the cultural aspects of lean, where employee involvement and empowerment are critical.
Challenges and Controversies
While lean manufacturing holds promise, it's not without controversy. Some critics argue that lean systems can become rigid and stifling over time, as evidenced by certain inefficiencies within older Toyota plants. Furthermore, a report by General Electric found that companies occasionally misuse lean terms without truly understanding the underlying principles, resulting in half-baked implementations and suboptimal outcomes.
The Role of Technology in Achieving Operational Excellence
Revolutionizing Business with Cutting-Edge Tech
In the fast-paced landscape of modern business, technology acts as a vital catalyst for achieving operational excellence. Innovatory solutions streamline processes, eliminating inefficiencies and paving the way for continuous improvement.
Process Automation: The Game Changer
Automation stands at the forefront of this transformation. According to McKinsey, firms integrating automation can reduce operational costs by up to 30%. By automating repetitive tasks, companies like Amazon have recalibrated workflow, focusing human efforts on strategic activities rather than mundane tasks, achieving superior productivity levels.
Data Analytics for Informed Decisions
Utilizing data analytics allows businesses to make informed, data-driven decisions. By crunching numbers, analyzing trends, and foreseeing bottlenecks, businesses can innovate and optimize continuously. Consider Toyota, whose integration of Big Data analytics into its lean manufacturing has cut down waste by 10%, setting a precedent for operational efficiency. Learn more insights here.
The Power of IoT in Monitoring and Maintenance
Internet of Things (IoT) solutions provide real-time monitoring, preempting downtimes and ensuring smoother operations. General Electric's use of IoT in predictive maintenance has resulted in 20% fewer maintenance costs, shedding light on how technology can revolutionize operational sustainability.
Enhancing Customer Experience Through Technology
Technological advances are not merely confined to backend operations; they trickle down to customer-facing facets, enhancing customer satisfaction. Tools like CRM systems and AI-driven chatbots lead to seamless, personalized customer interactions, improving overall service quality. Companies adopting robust CRM systems have seen a 25% boost in customer retention, proving the undeniable advantage of tech in achieving operational excellence.
Case Study: Chevron's Tech-Driven Success
Chevron is a shining star when it comes to leveraging technology for operational excellence. Implementing AI, the energy giant has optimized drilling operations, reducing downtime by 15% and significantly cutting operational costs.
As we continue, it is essential to understand the principles behind achieving such excellence. You can learn more about the core principles from our article on strategic insights into packaged goods for a broader perspective.
Case Studies: Companies Excelling in Operational Excellence
Toyota: Pioneer of Lean and Operational Efficiency
Toyota is the undisputed champion of lean manufacturing and a poster child for operational excellence. The company revolutionized the automotive industry with the Toyota Production System (TPS), a methodology based on two core principles: just-in-time and jidoka. As a result, Toyota achieved a 21.2% improvement in operational efficiency, as reported by the Toyota Global Website.
Amazon's Relentless Focus on Continuous Improvement
Amazon's success can be largely attributed to its commitment to continuous improvement and customer satisfaction. The e-commerce giant employs a strategy of operational excellence that emphasizes speed, efficiency, and innovation. According to a report by McKinsey, Amazon's operational efficiency has helped the company achieve a 38% increase in order fulfillment speed, significantly enhancing customer experience.
Chevron: Implementing Operational Excellence through the Shingo Model
Chevron has adopted the Shingo Model to drive continuous improvement and operational excellence initiatives. Chevron reported a 15% reduction in operational costs after integrating Shingo’s principles into their organizational culture. This success story was highlighted in a report by the Shingo Institute.
Motorola's Journey with Six Sigma
Motorola was instrumental in developing and popularizing Six Sigma methodologies to enhance quality and performance. By focusing on reducing process variation and defects, Motorola achieved significant gains in operational efficiency. A detailed study by the Institute of Six Sigma revealed that Motorola saved upwards of $17 billion over a span of 20 years, thanks to Six Sigma processes.
GE's Operational Excellence through Process Mining
General Electric (GE) leverages advanced process mining technologies to drive operational efficiency and uncover inefficiencies in manufacturing processes. GE’s use of technology enabled them to identify process bottlenecks and improve efficiency by 12%, according to an internal report published by GE.
The Impact of Continuous Improvement on Customer Satisfaction
Continuous Improvement: The Catalyst for Customer Satisfaction
Operational excellence isn't a one-time fix; it's a continuous journey of improvement that deeply affects customer satisfaction. In fact, 89% of customers switch to a competitor after a poor experience, making ongoing improvements crucial for retaining clients (PwC, 2020).
The Role of Employee Involvement
Engaged employees are more likely to commit to continuous improvement initiatives. A Gallup study found that businesses with highly engaged teams realize a 21% increase in profitability and a 17% increase in productivity. This is key in ensuring that processes remain effective and customer issues are swiftly addressed.
Applying Lean Principles to Enhance Customer Experience
Lean manufacturing has shown astounding results in operational improvement. Take Toyota, the pioneer in lean manufacturing; their dedication to minimizing waste and maximizing efficiency has led to an unbroken record of high customer satisfaction. Lean principles such as continuous improvement (Kaizen) and just-in-time production keep customer needs at the forefront.
Data-Driven Decision-Making
Companies that utilize data-driven approaches see a 23% increase in operating margins (McKinsey, 2022). By continually analyzing customer feedback and operational data, businesses can make informed improvements to both their processes and customer service strategies. For more on this, see this illuminating article on performance indicators.
Quality Management Systems
Quality isn't just about product excellence; it's about meeting customer expectations consistently. W. Edwards Deming, a key figure in quality management, advocated for continuous improvement and the role of management in fostering a culture that prioritizes quality. Deming’s principles are alive in today’s successful companies, emphasizing the need for a holistic approach to quality that includes customer feedback loops and rigorous testing protocols.
Case in Point: Amazon's Relentless Focus on Improvement
Amazon, a titan in operational excellence, continually evolves its processes to delight customers. From optimizing the supply chain to implementing advanced technology like AI and machine learning, Amazon ensures that each customer interaction is seamless. They even leverage process mining to identify bottlenecks and inefficiencies, aiming for constant enhancement of the customer experience.
Benefits Beyond Customer Satisfaction
Continuous improvement not only boosts customer satisfaction but also drives operational efficiency and innovation. Companies that embrace this mindset often find reduced costs, higher employee morale, and an agile organizational culture. According to the Shingo Institute, those who implement the Shingo Model see not only improved operational performance but also a more engaged and satisfied workforce.
Conclusion: The Unending Journey
In essence, the impact of continuous improvement on customer satisfaction is profound and multifaceted. By fostering a culture of ongoing enhancement, businesses not only meet but often exceed customer expectations, creating long-term loyalty and sustainable success. The philosophy of continuous improvement integrates deeply with various principles of operational excellence, forming a solid foundation on which to build a truly customer-centric organization.
Leveraging the Shingo Model for Organizational Success
Unlocking Operational Excellence with the Shingo Model
Operational excellence is not just a buzzword; it's a blend of effective principles and disciplined execution that drives businesses towards outstanding performance. The Shingo Model stands out as a beacon for organizations striving for improvement operational excellence.
The Essence of the Shingo Model
The Shingo Model is grounded in principles operational excellence. Created by Dr. Shigeo Shingo, a pioneering figure in Lean Manufacturing and Toyota Production System, his model prioritizes culture continuous improvement and lays down core principles operational. These principles guide organizations towards achieving long-term sustainable excellence operational.
Dr. Shigeo Shingo emphasized the need to align systems with operational excellence principles such as respect for every individual, focusing on process not results, and ensuring quality at the source. He believed that when these principles are woven into the fabric of an organization's culture, they pave the way for exceptional business outcomes.
Implementing the Shingo Model: Keys to Success
Successfully leveraging the Shingo Model requires understanding its core principles operational and applying them consistently. Let's take a closer look at how companies can integrate this model to achieve operational excellence:
- Creating a Respectful Culture: Engage employees by fostering a respectful work environment. A study from McKinsey revealed that companies with a strong focus on employee engagement saw a 21% increase in productivity.
- Continuous Improvement: Embed continuous improvement operational. According to the Institute for Operational Excellence, organizations that emphasize continuous improvement see a 20-30% reduction in operational costs over three years.
- Ensuring Quality at Source: Instill a quality-first mentality. Amazon's implementation of quality controls at various stages of their process significantly reduced defect rates.
Real-World Application: Chevron
Chevron's implementation of the Shingo Model is a perfect case study. Their adherence to the Shingo principles operational excellence initiatives resulted in winning the coveted Shingo Prize. Chevron's focus on operational improvements, employee empowerment, and quality at the source led to a 15% increase in overall operational efficiency.
By adopting a holistic strategy that emphasizes people, processes, and continuous improvement, Chevron achieved operational excellence, setting a benchmark in their industry.
The Shingo Model and Customer Experience
Customer satisfaction is the ultimate proof of operational excellence. Companies embracing the Shingo Model see marked improvements in their customer experience. A report by the Shingo Institute showcased companies with operational excellence goals witnessing a 25% rise in customer satisfaction within two years.
Expert Insights
Henry Ford once said, "Quality means doing it right when no one is looking." This aligns perfectly with the Shingo Model, which seeks excellence continuous improvement in unseen processes to achieve visible successes. W. Edwards Deming, another luminary in quality management, emphasized that consistent quality improvement leads to better products services and enhanced customer experience.
The Shingo Model isn't just a set of guidelines but a proven framework for achieving operational excellence through meticulous application of its core principles operational. By adopting this model, organizations can experience transformative improvements in their processes, employee engagement, customer satisfaction, and overall business performance.
Integrating Six Sigma for Quality and Performance Enhancement
Six Sigma: A Game-Changer in Quality and Performance
When it comes to quality and performance, Six Sigma stands out as a robust methodology. Pioneered by Motorola and embraced by giants like General Electric, it has become synonymous with excellence. The core aim of Six Sigma is to reduce variability in business processes, leading to fewer defects and higher customer satisfaction.
The DMAIC Framework: Structuring Improvement
Six Sigma follows the DMAIC framework (Define, Measure, Analyze, Improve, Control). This structured approach helps companies identify and eliminate defects in their processes:
- Define: Establish the project goals and customer deliverables.
- Measure: Collect data and set baseline metrics.
- Analyze: Identify root causes of defects and issues.
- Improve: Implement solutions to address the root causes.
- Control: Sustain improvements through monitoring and control systems.
Case Study: General Electric
General Electric (GE) is a classic example of Six Sigma's powerful impact. When Jack Welch, then CEO of GE, adopted Six Sigma, the company saw a significant improvement in quality across all its processes. By 1999, GE reported $2 billion in savings attributed to Six Sigma initiatives. Welch himself stated, "The benefits of Six Sigma far exceeded my expectations."
Real-World Impact: Improved Metrics
Six Sigma has shown tangible results in various sectors:
- Motorola: Saw a 20% increase in profits due to defect reduction.
- Honeywell: Achieved $600 million in savings by applying Six Sigma methodologies.
Integration with Lean Manufacturing
Lean Six Sigma combines Lean Manufacturing principles with Six Sigma tools, focusing on both waste reduction (Lean) and defect reduction (Six Sigma). This synergy provides a comprehensive approach to operational improvement. For instance, Toyota, a leader in Lean, integrates Six Sigma to enhance production efficiency further.
Expert Insights: Dr. Shigeo Shingo
Dr. Shigeo Shingo, a key advocate of Lean principles, once said, "The most dangerous kind of waste is the waste we do not recognize." By merging Lean and Six Sigma, organizations can pinpoint and eliminate both visible and hidden inefficiencies, achieving operational excellence.
The Future of Operational Excellence: Trends and Predictions
Embracing New Technologies for Operational Excellence
In the continuous improvement and operational excellence space, technology isn’t just a tool—it’s a game-changer. With 65% of companies emphasizing digital transformation as a core strategy, technology is at the forefront of achieving operational excellence.
Adoption of AI and Machine Learning in Operations
AI and Machine Learning have moved from buzzwords to actionable assets in operational excellence initiatives. McKinsey reports that 54% of executives say that AI has increased productivity in their operations. Companies like Amazon and General Electric are leveraging AI to streamline processes, reduce waste, and predict maintenance issues before they occur, proving AI’s significant impact on operational efficiency.
IoT and Real-time Data for Process Improvement
Increasing operational excellence means making your processes smarter and more connected. The Internet of Things (IoT) is playing a pivotal role. For example, Chevron uses IoT to monitor its equipment, ensuring optimal performance and minimizing downtime, leading to 98% availability of critical machinery. This level of real-time data enables quick decision-making and enhances the quality of operational processes.
The Power of Robotics and Automation
Robotics and automation are crucial in achieving operational efficiency. Toyota, a pioneer in lean manufacturing, uses robotics extensively, which has led to a 20% reduction in operational costs and a remarkable consistency in product quality. Automation reduces human error, speeds up production, and allows companies to allocate human resources to more strategic tasks.
Big Data and Predictive Analytics for Sustained Improvement
Operational excellence isn't a one-time achievement; it’s a long-term commitment. Big data and predictive analytics provide insights that spur sustained improvement. According to a report by the Institute for Operational Excellence, companies utilizing big data in their operational strategies can achieve up to 30-40% increase in operational efficiency. Procter & Gamble, for example, leverages big data analytics to optimize their supply chain and reduce lead times significantly.
The Role of Cloud Computing in Business Transformation
Cloud computing is revolutionizing the way businesses approach operational excellence. By adopting cloud services, companies can enhance collaboration, flexibility, and agility. The Shingo Institute highlights that businesses adopting cloud-based solutions have seen a 25% reduction in IT costs and improved work processes. Firms like McKinsey point out the transformational impact of cloud computing on operational workflows, enabling real-time updates and coordinated efforts across global operations.
Cybersecurity: Safeguarding Your Operational Excellence Initiatives
As businesses integrate more technology into their operations, cybersecurity becomes critical to protect data integrity and operational continuity. According to IBM, the average cost of a data breach is $3.86 million. Therefore, robust cybersecurity measures are essential for maintaining uninterrupted operations and achieving long-term operational excellence.