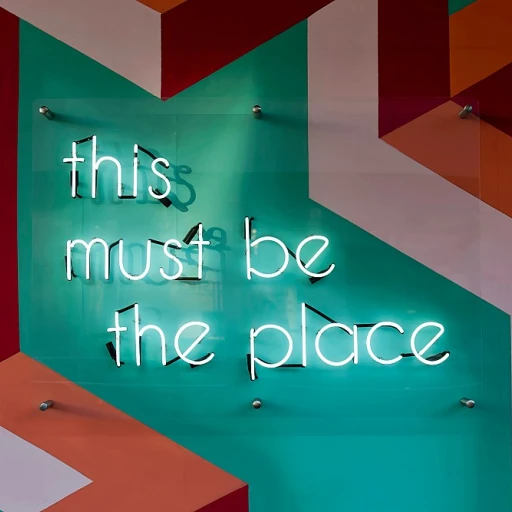
Defining the Quality Quotient in Business
Understanding the Quality Quotient
When we talk about the backbone of a successful business, quality often shines as the unsung hero. It's the invisible thread that holds together customer trust, brand reputation, and operational excellence. Steering this ship is the quality quotient – a term that encapsulates an organization's inherent ability to consistently produce value that meets or exceeds customer expectations.
Drilling down into the essence of quality, it's not just the end product that's scrutinized. Every touchpoint in the manufacturing chain, every cog in the corporate wheel must spin with a synchronized commitment to excellence. And how do we measure this commitment? It's through meticulously designed systems and processes that aim for continuous and quality improvement—a journey rather than a one-time check-off.
Elements of a Robust Quality Management System
Within the ambit of quality management lies the concept of the Quality Management System (QMS). A QMS is a formalized system that documents processes, procedures, and responsibilities for achieving quality policies and objectives. Here, decision-making is not left to chance but informed by evidence-based decision making. Leveraging data and quality management software, organizations ensure that every product or service aligns with their benchmark for excellence.
Take the story of Toyota, for instance. The Japanese carmaker's legendary manufacturing principles revolutionized not just the automobile industry but how we perceive quality at large. Toyota's approach intertwines quality with strategy, asserting that maintaining high standards is an integral part of the business model, not merely a compliance tick-box.
Quality in business isn't just about meeting specifications; it's about threading customer satisfaction through the fabric of an organization's culture. For example, an increasing number of organizations are turning to the International Organization for Standardization (ISO) to chart their quality journey. The principles of ISO quality management provide a universal language of improvement, be it through ISO 9001's guidelines or sector-specific standards that fine-tune the focus to particular industry demands.
Furthermore, the rise of labor innovations has ushered in new dimensions of quality management, from leveraging digital tools to integrating sustainable and ethical practices in the supply chain.
Measuring Success: Metrics that Matter
Progress in managing quality isn't hinged on guesswork. Quantifiable metrics such as defect rates, turnaround times, and customer feedback scores paint a picture of where a company stands and where it needs to go. Industry reports suggest that companies investing in advanced quality management systems can see customer satisfaction rates improve by as much as 20%, while operational efficiency can receive a boost in productivity by up to 15%.
At the heart of it all, the goal is a business environment where quality isn’t just a department but a language spoken fluently across the enterprise. And this approach speaks volumes, not only in the symphony of daily operations but also in the lasting impression left with customers who come to associate a brand synonymous with trust and excellence. Therein lies the true art of excellence in quality management.
Unpacking ISO Standards: The Blueprint of Quality Excellence
A Guided Tour Through ISO Standards
When it comes to quality management, strategic imperatives for modern organizations often anchor around the adoption of International Organization for Standardization (ISO) standards. ISO frameworks are globally recognized for setting the bar for quality. Delve a little deeper, and you'll find that ISO 9001, in particular, is not just a badge of honor; it's akin to a DNA blueprint for injecting quality into the very core of an organization.
Crunching the Numbers: ISO's Global Influence
ISO has published over 22,000 standards, with ISO 9001 being among the most prevalent, implemented by over one million organizations in 178 countries. This mass adoption underscores the standard's capacity to streamline processes and enhance customer satisfaction. A staggering 87% of companies certified in ISO 9001 testify to its significant impact on their business operations, according to the ISO Survey of Management System Standard Certifications.
Crafting Quality with ISO Guidelines
Quality management systems (QMS) that adhere to ISO standards help organizations espouse a culture of continuous improvement. By highlighting deficiencies and celebrating strengths, a well-oiled QMS fosters an environment where quality improvement methods aren't just a checkbox on a compliance list—they're enablers of innovation and efficiency.
Expert Voices on ISO Standards
Renowned quality gurus like W. Edwards Deming and Joseph Juran have long promoted the principles that underpin ISO standards—focused on customer quality and the philosophy of continuous improvement. Deming's Plan-Do-Check-Act cycle is implicitly embodied in the continuous loop of improvement that ISO standards champion, bolstering the organization's ability to adapt and thrive amidst evolving business climates.
ISO and Customer Trust
At the heart of ISO quality management principles lies the goal of exceeding customer expectations. A study on the impact of ISO 9001 on customer satisfaction highlights that organizations adhering to ISO standards often see a direct correlation between their quality management efforts and customer loyalty—after all, quality is a language that every customer speaks.
Integration and Synergy with ISO 9001
Harmonizing the myriad aspects of an organization—be it operations, human resources, or procurement—is no small feat. ISO 9001 provides a management framework that promotes synergy, thereby enhancing an organization's operational resilience. By standardizing quality measures, businesses can wield greater control over variability, driving quality from top-tier leadership down to the operational bedrock.
The Evidence-Based Backbone of ISO
In a sphere where gut-feeling often sways decision-making, ISO standards are a bastion of evidence-based practices. By calling for data-driven approaches and meticulous record-keeping, ISO steels organizations against the winds of change, instilling a culture where informed decisions take precedence over ad-hoc judgment calls.
Total Quality Management: From Japanese Roots to Global Fruit
The Evolution of Total Quality Management
Tracing the lineage of Total Quality Management (TQM) brings us to the shores of Japan, post-World War II. It was in this period of economic recovery that visionary Japanese business leaders and quality gurus, notably W. Edwards Deming and Kaoru Ishikawa, crystallized principles of quality control into what would become a transformative business philosophy. TQM evolved from statistical quality control methods that had been developed by Walter A. Shewhart in the earlier decades. This comprehensive system emphasized company-wide quality control, where all employees from top management to the shop floor workers participate in continual improvement practices. Total quality management became synonymous with superior product service and unwavering customer satisfaction, setting Japanese products apart on the global stage.
Driving Forces Behind TQM Adoption
As organizations internationalized, the need to establish globally recognized benchmarks for quality improvement led to the integration of TQM into various sectors. From Toyota's famous 'Toyota Production System', which embodied TQM and operational excellence, to other industries adopting these practices for their process enhancement, TQM became central to the competitive advancement of businesses. This was underscored by the rise of international frameworks like ISO quality standards, furthering the case for a structured approach to quality. The core tenets of TQM—customer-centricity, continuous improvement, and a systemic approach to problem-solving—remain as relevant today as ever before, merging the Japanese business philosophy with the International Organization for Standardization's drive for quality excellence.
Quantitative Impact and Expert Validation
Statistically, the influence of TQM is evident. Studies have shown that the implementation of TQM practices have led to significant improvements in operational performance. One such example comes from a research article in the Journal of Operations Management, which reported that TQM practices are associated with a median improvement of 48% in customer satisfaction, 34% in overall financial performance, and 45% in employee relations. Experts in the field, including champions like Deming and Juran, have written extensively, leaving behind a legacy of literature such as Deming's Out of the Crisis and Juran's Juran's Quality Handbook, providing the blueprint for effective quality management.
Total Quality Management in Action: Case Studies
Turning to real-world applications, one can find a plethora of TQM success stories. For instance, the FDA's endorsement of TQM principles in regulatory affairs illustrates the cross-industry relevance of quality systems. Additionally, enterprise quality management in companies like Xerox and Ford, which embraced Deming's 14 Points, exemplifies how TQM can transform business processes and culture. These historical examples not only validate the effectiveness of TQM strategies but also serve as educational cases for present-day businesses aspiring towards quality excellence.
To truly master the strategic keys in business, including those related to quality management, decision-making, and negotiation, exploring insights at C-Suite Strategy can prove invaluable for modern leaders.
The Contemporary Relevance of TQM
Despite its historical roots, TQM has not remained static. Adapted and revitalized for the digital age, TQM now often includes the utilization of quality management systems (QMS) software, blending traditional quality management tqm with digital innovation. This synergy ensures that the principles of TQM continue to empower organizations in their quest for top-tier quality management. Data-driven decision-making has woven itself into the TQM fabric, reinforcing the role of evidence-based decision processes in achieving excellence.
In light of continuous quality improvement methods and a more pronounced emphasis on management quality, the modern TQM approach reflects a depth of understanding for today's dynamic market needs. It stresses not only the value of historical perspectives and foundational quality management principles but also the importance of evolving with technological advancements and changing consumer expectations.
Navigating Quality in the Digital Era: QMS Software Revolution
Embracing the Digital Shift: Leveraging QMS Software for Streamlined Operations
In the realm of strategic pathways to economic elevation, the adoption of Quality Management System (QMS) software stands out as a transformative milestone. This digital leap promises to redefine how organizations approach quality assurance and quality control, bringing about an era of efficiency and precision.
QMS software tools are designed to integrate the multifaceted aspects of managing quality within an organization into a cohesive framework. Through automation and real-time data analytics, these systems facilitate continuous improvement and foster an environment where decision making is evidence-based. As per a study by Grand View Research, the global quality management software market size was valued at USD 9.7 billion in 2021 and is expected to expand at a compound annual growth rate (CAGR) of 9.8% from 2022 to 2030, showcasing the sector's robust growth potential.
Enhancing Decision-Making with Quality Data Integration
The heart of a successful QMS is its ability to streamline data management and flow. This ensures not just the accessibility of information but also its accuracy and relevance. Modern QMS software integrates total quality management (TQM) principles with advanced analytics allowing organizations to pinpoint inefficiencies and to capitalize on opportunities for quality improvement.
Experts like W. Edwards Deming and Walter A. Shewhart, who have greatly influenced the quality management practices, would have appreciated today's software capabilities to predict issues before they become problems through proactive quality planning and analytics.
The Convergence of QMS and Regulatory Compliance
For industries subjected to stringent regulations, such as pharmaceuticals and food and beverage, overseen by entities like the FDA in the United States, QMS software has proven invaluable. These platforms support adherence to regulatory requirements by maintaining essential documentation and traceability through document control features. By doing so, businesses can navigate the complexities of compliance with increased confidence while minimizing risks of non-conformity.
Cutting-edge Innovations: AI and ML in QMS Software
Emerging technologies like Artificial Intelligence (AI) and Machine Learning (ML) are setting the stage for the next quantum leap in quality management systems. With predictive analytics and intelligent automation, these innovations enhance a company's capability to deliver superior product service. Additionally, AI-driven insights are revolutionizing the TQM landscape by offering foresight into customer satisfaction drivers and facilitating a more proactive approach to quality management.
The integration of AI in QMS is not without its challenges. Issues concerning data privacy, the complexity of algorithms, and the need for skilled personnel to manage these sophisticated systems invite a measured approach to adoption. Nevertheless, the benefits of AI-infused QMS platforms suggest a significant competitive advantage for early adopters who navigate these waters successfully.
Indeed, the digital transformation in quality management is as much about the technology as it is about the cultural shift within organizations. Embracing these advancements necessitates a change in mindset, from the C-suite to the operational level, to ensure that everyone recognizes the essential role of quality in the company's strategic framework.
In summary, the digital era ushers in a revolution in QMS software, empowering businesses with tools for unparalleled quality management and regulatory compliance. As these technologies continue to evolve, they will undoubtedly play a pivotal role in shaping future quality management practices and organizational success.
Empowering the Customer-Centric Approach in Quality Management
Elevating Customer Satisfaction to New Heights
Understanding that customer satisfaction is not just a goal but a guarantee for sustainability in today's market is pivotal. The era when businesses dictated market trends is being outshined by an era where customer feedback forms the backbone of quality assurance. In this landscape, quality management takes on a more dynamic role, harmonizing the customer's voice with the heartbeat of a company’s operations. Through quality management systems (QMS), organizations are now embracing the practice of infusing customer feedback into all levels of their product service lifecycle.
Quality as a Dialogue, Not a Monologue
Characterized by a proactive quest for customer feedback, modern QMS solutions have transcended their traditional boundaries. From social media analytics to sophisticated customer survey tools, businesses tap into rich data reserves to align their products services with customer expectations. By integrating tools for effective quality management, they turn every customer interaction into a learning opportunity, ensuring continuous improvement in quality delivery.
Case Studies: The Proof is in the Pudding
Real-world success stories underscore the value of a customer-centered quality approach. For instance, companies like Toyota, a vanguard of the revered Total Quality Management (TQM) philosophy, show how listening to the end-user enhances product quality and boosts business prosperity. Similarly, tech giants use data-driven customer insights to refine user experience continuously, often leading to increased loyalty and advocacy. The numbers also sing the same tune, with organizations that excel at customer experience outperforming their competitors by nearly 80% in revenue growth, according to a report by the American Customer Satisfaction Index (ACSI).
Turning Feedback into a Strategic Asset
In the engine room of quality improvement methods lies the ability to transform customer feedback into actionable intelligence. With advances in management software, businesses can now implement a systematic approach to collecting, analyzing, and responding to customer input. Quality management principles encourage the use of evidence-based decision-making, ensuring that strategies are customer-focused and results-driven. The International Organization for Standardization (ISO), through ISO quality management standards, reinforces the importance of customer satisfaction in quality planning processes.
The Synergy of TQM and Technology
The embrace of TQM principles, coupled with state-of-the-art quality management software, is like threading a needle with surgical precision—it’s about enhancing quality while maintaining a seamless and personal customer relationship. The integration of real-time feedback systems into QMS platforms exemplifies an enterprise quality management ethos that many organizations aspire to achieve. With every customer interaction seen as a jewel for improvement, the depth and breadth of quality management leap dramatically, transforming passive metrics into a treasure trove of insights for continuous enhancement.
Empowerment through Quality and Control
There’s wisdom in the adage, “The customer is always right,” but there’s genius in the practice of customer-centric quality control. Whether it’s through user-friendly return policies, responsive customer service, or transparency in quality improvement processes, businesses today are not just assuring quality; they are co-creating it with their customers. Giving customers a seat at the decision-making table also fosters trust, making it a strategic maneuver that can lead to unshakeable brand loyalty.
Conclusion
In sum, riding the wave of customer-centric approaches in quality management means more than just meeting expectations; it’s about exalting the customer’s role as a co-pilot in the journey toward quality excellence. A testament to this is the way organizations with robust management systems and a fervent focus on customer satisfaction continue to carve their niches in the annals of business success. Indeed, when it comes to quality, businesses can no longer afford to just build it and hope they will come; they have to listen, adapt, and improve continuously.
Process Excellence: Engineering Efficiency with Document Control
Forging Ahead with Process Excellence
Imagine walking into a world-class orchestra playing a symphony without a conductor or a concertmaster. The result would likely be a cacophonous medley rather than a harmonious masterpiece. Process excellence in quality management operates much like the conductor of an orchestra. It ensures that each element and action within the organization's processes are fine-tuned, synchronized, and executed to the highest standards of quality.
The Role of Document Control in Streamlining Processes
At the heart of process excellence lies document control – the meticulous orchestration of paperwork, electronic files, and revision histories that form the foundation of a robust quality management system. It’s not just about having all your ducks in a row; it’s about knowing each duck, its journey, and ensuring they all head in the right direction. A recent study from the American Society for Quality (ASQ) showed that poor document control could result in compliance issues for 60% of organizations, highlighting the critical need for effective management of documents.
Consider Toyota’s legendary production system, which hinges on kaizen, or continuous improvement. By maintaining rigorous control over their process documentation, Toyota ensures that improvements are systematically documented, shared across the organization, and become a permanent part of the process. This dedication to document control is a living testament to its importance in achieving process excellence.
Leveraging Quality Data to Drive Decision-Making
In the arena of quality management, data is king. Comprehensive data gathering delivers actionable insights that drive continuous improvement and strategic decision-making. Moreover, it is evidence-based decision-making that sets the benchmark for industry excellence. A survey by ASQ revealed that organizations with a high level of quality data integrity achieved an average customer satisfaction rate 15% higher than those without.
Effective quality management leverages metrics not just for the sake of having numbers to present at board meetings but for identifying patterns, predicting potential issues, and crafting solutions to enhance system efficiency. When quality data is meticulously harnessed, it enables an organization to navigate its market with the precision of a GPS-guided system.
Embracing Quality Improvement Methods
Embedding quality at every level of the production and management processes ensures that nothing is left to chance. Methods like Six Sigma, Lean, and ISO’s Quality Management Principles are like the brushstrokes of a master artist—each one contributes to the greater picture of organizational excellence. For example, within the realm of document control, employing the Six Sigma DMAIC (Define, Measure, Analyze, Improve, Control) roadmap can lead to radical improvements in accuracy and reduction in cycle time for document processing.
Fredrick Winslow Taylor, a forefather of quality control, couldn't have put it more succinctly when he advocated for stringent standards that result in predictable, repeatable processes. This approach is echoed by quality management scholars and practitioners such as W. Edwards Deming and Walter A. Shewhart, who emphasized the importance of well-defined processes for consistent quality.
Quality as Strategy: Integrating QMS into Organizational DNA
Embedding Quality at the Heart of Corporate Culture
Quality shouldn't just be a checkpoint or a department within an organization; it's a strategic asset that must permeate every aspect of a business's operations. This holistic belief is echoed by quality management principles which advocate for a quality-centric culture as the foundation for sustained success. A report by the American Society for Quality (ASQ) clearly indicates that companies with a deeply embedded quality culture have shown improvements in customer satisfaction rates and operational efficiency.
Elevating Quality Beyond Compliance
Moving from mere compliance to a strategic emphasis on quality requires a shift in mindset. It's about evolving from compliance-focused quality assurance to an integrated approach involving everyone's commitment. Toyota's legendary production system illustrates the power of this holistic approach, leading to substantial improvements in production efficiency and reducing waste, without compromising on quality—a practice that has inspired countless businesses worldwide.
Quality as an Innovation Catalyst
Quality management systems (QMS) aren't just about maintaining standards; they can be powerful drivers of innovation. In industries regulated by the FDA in the United States, adherence to quality isn't just mandatory, it's a key competitive differentiator. Brands that leverage their QMS for continuous improvement often find themselves ahead of the curve, turning regulatory challenges into opportunities for innovation.
Continuous Improvement as a Strategic Imperative
In the spirit of TQM and legends like W. Edwards Deming and Walter A. Shewhart, today's successful businesses view quality improvement as a never-ending journey. Enterprises employing continuous improvement methodologies witness ongoing enhancements in product service and process efficiency. It's not surprising to find in case studies that lean organizations adopting continuous improvement as a strategic item have outperformed their peers in terms of agility and responsiveness to market changes.
Data-Driven Quality Decisions
Decision making grounded in solid data is the backbone of effective quality management. This evidence-based decision-making practice stands at the forefront of ISO quality management principles. Organizations excel in quality management when they use precise data to drive their strategies—be it customer feedback loops, production metrics, or service delivery performance indicators. An ISO quality management system embeds these data points into the fabric of an organization, ensuring decisions are informed, measurable, and lead to genuine improvements.
Total Quality as Organizational Wisdom
A study by the International Organization for Standardization (ISO) has shown that embedding total quality management (TQM) into the DNA of an organization does not just enhance operational processes but also nurtures a mindset of quality across the board. This approach resonates with the Japanese business philosophy of 'Kaizen', which emphasizes continuous, incremental improvement. It's a level of sophistication in strategy that shapes not only what a company does but also what it is.
Quality Management Software: A Strategic Enabler
Enterprise quality management software has emerged as a crucial tool for companies seeking to integrate quality deeply into their strategic planning. With features like document control, process mapping, and quality analytics, these systems support the kind of agility needed in modern business landscapes. They enable an organization to monitor quality in real-time and facilitate swift, strategic responses to any issues that arise, ensuring management processes are more dynamic and streamlined.
The Future of Quality: Predicting Trends in Management Practices
Decoding the Future of Quality Management
Within the fluid dynamics of modern business, quality management has emerged as a pivotal engine for sustainable success. The emphasis on continuous improvement and customer satisfaction has led organizations to pivot towards innovative strategies, striving to future-proof their operational processes. In this quest for excellence, tracking the evolution of quality management practices becomes vital for staying competitive and meeting the high standards of the market.
Leaner, Smarter Quality Management Systems
Quality management systems (QMS) are no longer static entities but are evolving into more agile and intelligent frameworks. The integration of advanced analytics and machine-learning capabilities within QMS software enables predictive quality, where data-driven foresight helps organizations to prevent defects and non-compliance issues proactively. By leveraging total quality management (TQM) principles alongside new technological advancements, businesses can attain a more nuanced and forward-looking approach to quality assurance.
Customization and Personalization through AI
The deployment of AI in quality management is pioneering a shift toward highly customized and personalized product service solutions. With AI's capacity to analyze copious amounts of data, companies can now tailor products and services to match individual customer preferences, thereby enhancing customer satisfaction levels significantly. This personal touch is vital in today’s market, where product differentiation is often a key factor in winning customer loyalty.
Synergy of IoT and Quality Assurance
The proliferation of the Internet of Things (IoT) holds the promise of bringing a new dimension to quality assurance and control. IoT technology facilitates real-time monitoring and optimization of manufacturing and business processes. It provides an unprecedented level of visibility and control over quality improvement methods, advocating for a highly responsive and interconnected QMS interface.
Emphasis on Cybersecurity within Quality Paradigms
In the digital domain, protecting the integrity of data and processes is synonymous with upholding quality standards. As such, cybersecurity measures are becoming deeply ingrained within the quality management process. Organizations are recognizing the need to defend against cyber threats proactively, ensuring that both their data and their customers’ privacy are safeguarded, which in turn reinforces the foundation of trust essential to any quality-centric organization.
Driving Sustainability in Quality Endeavors
An emerging trend in quality management is the integration of sustainability goals. Companies are learning to align their quality improvement methods with environmental and social governance criteria. This merger illustrates a holistic vision where quality extends beyond the product or service itself, resonating with wider corporate responsibility and consumer values.
Integration of Compliance with Innovation
Compliance is a cornerstone of effective quality management, which can sometimes seem at odds with the rapid pace of innovation. However, forward-thinking companies are architecting their management systems to be flexible and adaptable, effortlessly integrating regulatory requirements without stifling innovation. This agility ensures that they can respond to the changing landscape of both market demands and international standards for quality and safety, exemplified by dynamic regulatory guidelines such as those from the FDA or ISO.
To remain at the forefront of quality management practices, modern organizations invest in talent development, foster a culture of quality at all levels, and adopt cutting-edge technologies that drive data-focused, customer-centric outcomes. As this evolutionary landscape unfolds, attention to detail in quality planning, continuous improvement, and organizational agility will dictate the leaders in the game of quality excellence.